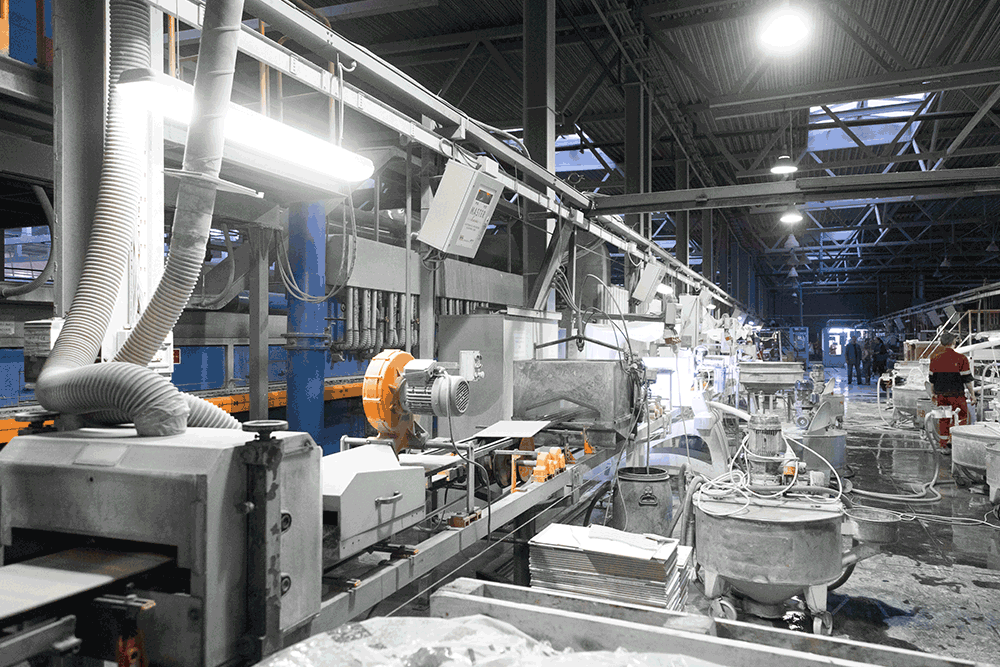
Services of Cement Industry
INTRODUCTION
In the cement industry, maintaining equipment reliability and minimising downtime are important for performance.
At Metatech, we understand the role that durability, efficiency, and uptime play in keeping your cement plant operations smooth and uninterrupted.
That's why our specialised coatings are designed to address your toughest challenges and extend the life of your components.
Introducing Metatech’s Specialised Coatings
Metatech offers a range of high-performance coatings specifically customised for the cement industry.These coatings protect your machinery and enhance performance, reduce wear and tear, and help you save on maintenance costs. Let’s explore our offerings in more detail.
Boiler Tube Coating with Twin Wire Arc Spray
Boiler tubes in cement plants endure harsh conditions, and Metatech's Twin Wire Arc Spray coating is designed to provide superior protection with minimal downtime. This coating is fast to apply and offers durability.- Porosity: Less than 8%, providing a dense and reliable surface.
- Adhesion: Up to 5000 psi, ensuring the coating remains firmly in place.
- Hardness: Between 55-60 HRC, offering protection against wear.
- Build-Up: Capable of reaching up to 500 micrometres, adding an extra layer of defence. The result?
Longer-lasting boiler tubes with fewer shutdowns, saving you time and money.
HVOF Spray: Next-Level Protection
For equipment exposed to the most extreme conditions, our High-Velocity Oxy-Fuel (HVOF) spray coating delivers an unparalleled level of protection. The HVOF spray is ideal for areas that demand more than conventional coatings:- Porosity: Less than 1%, ensuring a highly dense, durable coating.
- Adhesion: Up to 10,000 psi for sticking power.
- Hardness: Up to 65-70 HRC, providing the highest levels of protection.
- Smooth Surface: Minimises friction and wear, keeping equipment running efficiently.
This advanced coating solution is perfect for components that need the highest level of wear resistance and longevity.
Thermal Spray Aluminium Coating: High-Temperature Corrosion Resistance
Corrosion is a problem in areas like bag houses, chimneys, and pre-heaters.Our Thermal Spray Aluminium (TSA) coating offers superior corrosion resistance, even at high temperatures:
- Corrosion Resistance: Exceptional protection, even at elevated temperatures.
- Temperature Resistance: Effective up to 500 °C.
- Longevity: Lasts over 10 years, drastically reducing the need for frequent maintenance.
Ceramic and Tungsten Carbide Coatings
When extreme wear is a concern, especially for parts like pump sleeves, shafts, and textile mill rollers, Metatech's Ceramic and Tungsten Carbide coatings offer the perfect solution:- High-Temperature Resistance: Excellent for challenging environments.
- Increased Hardness & Wear Resistance: Extends the life of components.
- Chemical & Corrosion Resistance: Protects against harsh operating conditions.
These coatings ensure that your equipment remains functional for extended periods, even in the toughest environments.
Thermal Spray Zinc Coating for Structural Protection
Large structures such as reactors and risers face ongoing threats from corrosion. Metatech’s Thermal Spray Zinc (TSZ) coating offers an alternative to hot-dip galvanising. The coating can be applied on-site, regardless of the size of the component, providing:- On-Site Applicability: Suitable for large or complex structures.
- Corrosion Protection: Ensures long-lasting protection against environmental wear.
This makes TSZ a versatile and cost-effective solution for protecting large-scale infrastructure.
Bearing Journal Reclamation: Save Costs, Extend Life
Worn-out bearing journals no longer mean replacing entire shafts. Metatech’s coating process reclaims the size of the journals without affecting the base metal, saving you significant costs:- Low-Temperature Application: Ensures the base metal remains unaffected.
- Cost Savings: Avoid the expense of shaft replacement.
This process provides a reliable and cost-effective alternative to traditional methods like welding.
Why Choose Metatech?
Metatech has a proven track record of working with industry giants such as UltraTech Cement, Ambuja Cement, and Sanghi Cement.
Our 35,000 sq. ft. advanced workshop, equipped with 15 tons of EOT cranes and robotic coating technology, ensures that we can deliver the best quality coatings with minimal downtime.
Contact us today at www.thermalsprayworld.com to learn more about how we can help you improve your plant’s performance and durability.
For more details around the coatings, you can also follow our founder Bhavik Patel on LinkedIn.