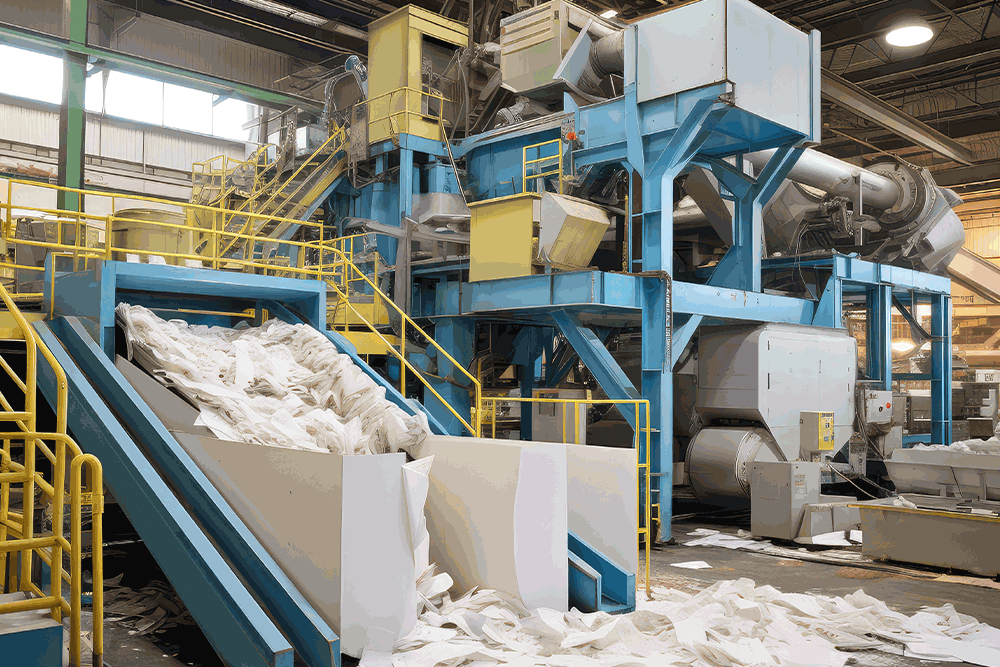
Role of HVOF Coating in Automotive
High-Velocity Oxy-Fuel (HVOF) coating is essential in the automotive industry. It enhances the durability, wear resistance, and performance of key components. Automotive parts operate under extreme conditions, including high friction, heat, and exposure to chemicals. HVOF coatings create a hard, dense surface layer that protects components from these challenges.
What is HVOF Coating?
HVOF stands for High-Velocity Oxy-Fuel. It is a thermal spray process used to apply protective coatings. The process involves heating coating materials like metal or ceramic powders with a fuel and oxygen mixture. The mixture is ignited, creating a high-speed jet of gas that propels the heated particles onto the component surface. The particles form a dense, tightly adhered coating.
HVOF coatings are known for their hardness, low porosity, and resistance to wear, corrosion, and heat. These properties make them ideal for automotive components that experience high stress.
Importance of HVOF Coatings in Automotive
Automotive components face constant wear, friction, and environmental exposure. Without protection, these parts degrade quickly, leading to performance issues and higher maintenance costs. HVOF coatings provide the following benefits:
- Wear Resistance: Moving parts like engine valves and suspension components face friction. HVOF coatings reduce wear, extending the lifespan of these parts.
- Corrosion Protection: Components exposed to moisture, salt, and chemicals, such as brake rotors, are vulnerable to corrosion. HVOF coatings create a barrier that prevents rust and chemical damage.
- Thermal Stability: Engine parts like pistons and turbochargers operate at high temperatures. HVOF coatings maintain their structure under heat, protecting these components.
- Improved Fatigue Life: Repeated stress cycles can cause parts to crack or fail. HVOF coatings reduce stress concentration points, lowering the risk of fatigue damage.
These benefits help automotive manufacturers meet performance and durability requirements while reducing the need for frequent repairs.
Applications of HVOF Coatings in Automotive
HVOF coatings are used across various automotive components to improve performance and longevity. Common applications include:
Engine Components
- Parts like pistons, valves, and cylinder liners experience high heat and friction.
- HVOF coatings protect these parts from wear, erosion, and thermal damage.
Brake Rotors
- Brake rotors are exposed to intense friction during braking.
- HVOF coatings enhance wear resistance and prevent rust formation, ensuring reliable braking performance.
Suspension Systems
- Suspension components like shock absorbers and struts face heavy mechanical loads.
- HVOF coatings reduce wear and protect against corrosion, improving system durability.
Transmission Parts
- Transmission gears and shafts endure high-speed rotation and friction.
- HVOF coatings increase wear resistance, reducing the risk of mechanical failure.
Exhaust Systems
- Exhaust components face heat, moisture, and chemical exposure.
- HVOF coatings protect against oxidation and thermal degradation.
Materials Used in HVOF Coatings
The choice of coating material depends on the application and required properties. Common materials include:
- Tungsten Carbide: Offers high wear resistance and is often used for brake rotors and transmission components.
- Chromium Carbide: Provides both wear and corrosion resistance. It is suitable for high-temperature applications like engine parts.
- Nickel-Based Alloys: Provide moderate wear and corrosion resistance. These alloys are often used on exhaust systems and turbochargers.
- Ceramics: Ideal for extreme heat resistance, making them suitable for engine and exhaust components.
Comparison with Other Coating Methods
HVOF coatings are often compared to other coating processes like plasma spray and flame spray. Here is how HVOF stands out:
- Higher Density: HVOF coatings have fewer pores, reducing the risk of corrosion and wear.
- Stronger Adhesion: The high velocity of the application process ensures a better bond to the component surface.
- Lower Oxidation: The HVOF process minimizes oxidation, preserving the coating material's properties.
While plasma spray can achieve higher temperatures, HVOF is preferred for applications requiring high wear resistance and strength.
Maintenance and Inspection of HVOF Coatings
Regular maintenance and inspection help ensure the long-term performance of HVOF-coated components. Automotive technicians check for signs of wear, cracking, and delamination. Early detection of damage allows for timely repairs, preventing more serious issues.
Common inspection methods include:
- Visual Inspection: Detects surface defects like cracks and peeling.
- Ultrasonic Testing: Identifies internal flaws and delamination.
- Adhesion Testing: Measures the strength of the coating bond.
Future Trends in HVOF Coatings
Research continues to advance HVOF technology. Emerging trends include:
- Advanced Materials: New materials with better thermal and mechanical properties are being developed.
- Automation: Automated HVOF systems improve consistency and reduce errors.
- Environmental Sustainability: Efforts to reduce emissions and waste in the coating process are increasing.
Conclusion
HVOF coatings provide essential protection for automotive components, enhancing durability, safety, and performance. By resisting wear, corrosion, and high temperatures, these coatings extend component lifespan and reduce maintenance needs. As technology advances, HVOF coatings will continue to play a critical role in the automotive industry.