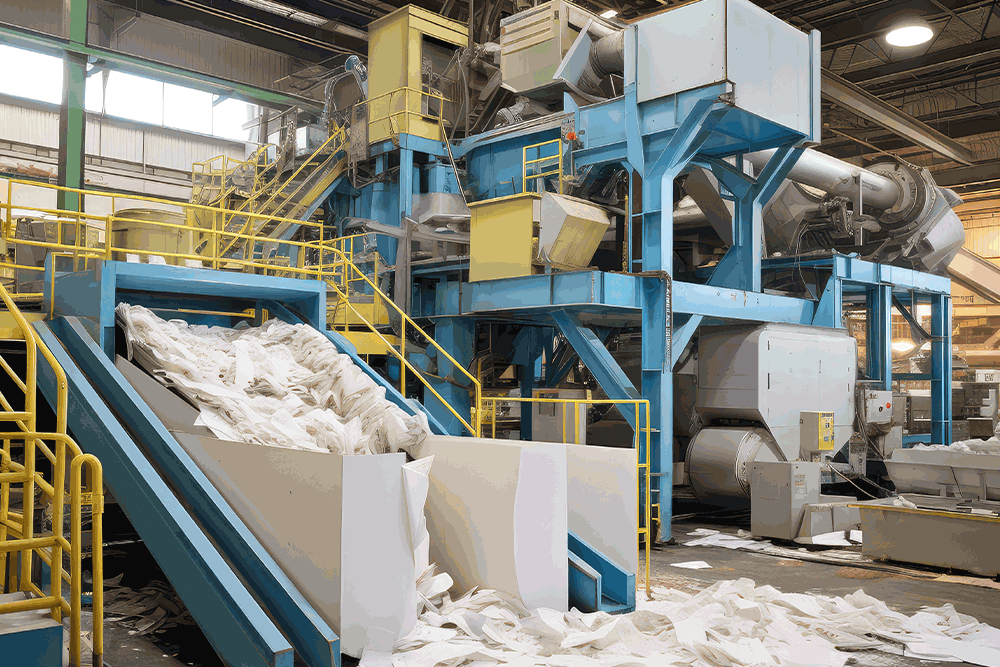
Role of HVOF Coating in Aerospace
High-Velocity Oxy-Fuel (HVOF) coating plays a crucial role in the aerospace industry. It improves the performance and durability of critical components like turbine blades, landing gear, and engine parts. Aerospace equipment operates under extreme conditions, making wear and corrosion resistance essential for safety and efficiency. HVOF coatings provide these protections by creating a hard, dense surface layer.
What is HVOF Coating?
HVOF stands for High-Velocity Oxy-Fuel. It is a thermal spray process that involves heating coating materials, such as metal or ceramic powders, using a fuel and oxygen mixture. The mixture is ignited, creating a high-speed jet of gas. This gas propels the coating particles onto the component’s surface. The high velocity compacts the particles, forming a dense, strong coating that adheres tightly.
HVOF coatings are known for their superior hardness, low porosity, and resistance to wear and oxidation. These properties make them ideal for aerospace components subjected to high stress and temperature.
Importance of HVOF Coatings in Aerospace
Aerospace components must withstand harsh environments, including high heat, friction, and chemical exposure. Without adequate protection, these parts degrade quickly, leading to performance issues or failures. HVOF coatings offer the following benefits:
- Wear Resistance: Components such as turbine blades and landing gear experience significant wear due to friction. HVOF coatings create a hard surface that reduces wear, extending component life.
- Corrosion Protection: Aircraft parts are exposed to moisture, chemicals, and salt in the atmosphere. HVOF coatings act as a barrier, preventing corrosion and chemical damage.
- Heat Resistance: Turbine blades and engine components operate at high temperatures. HVOF coatings maintain their integrity under extreme heat, protecting these parts from thermal damage.
- Improved Fatigue Life: Fatigue failure occurs when components crack or break after repeated stress cycles. HVOF coatings reduce surface stress concentrations, lowering the risk of fatigue damage.
These benefits help aerospace manufacturers meet stringent safety and performance standards while reducing maintenance and downtime.
Applications of HVOF Coatings in Aerospace
HVOF coatings are used in various aerospace applications to protect and enhance key components. Below are the primary applications:
Turbine Blades
- Turbine blades face high-speed airflow and extreme heat during engine operation.
- HVOF coatings protect these blades from oxidation, erosion, and wear.
- This protection ensures efficient engine performance and reduces maintenance costs.
Landing Gear
- Landing gear components endure heavy loads during takeoff, landing, and taxiing.
- They are also exposed to environmental factors such as water and salt.
- HVOF coatings enhance wear and corrosion resistance, preventing premature failure.
Engine Components
- Engine parts, including shafts, valves, and nozzles, experience both mechanical and thermal stress.
- HVOF coatings improve these parts’ ability to resist friction, erosion, and thermal degradation.
Hydraulic Cylinders
- Hydraulic systems play a critical role in controlling aircraft movements.
- HVOF coatings protect hydraulic cylinder surfaces from wear and corrosion, ensuring reliable operation.
Materials Used in HVOF Coatings
The choice of coating material depends on the application and the specific challenges the component faces. Common materials include:
- Tungsten Carbide: Provides excellent wear and abrasion resistance. It is often used for landing gear and hydraulic components.
- Chromium Carbide: Offers both wear and corrosion resistance. It is suitable for high-temperature environments, such as turbine blades.
- Nickel-Based Alloys: Provide good corrosion resistance and moderate wear protection. These alloys are used on engine components.
- Ceramics: Ideal for applications requiring high heat resistance, such as exhaust systems and combustion chambers.
Each material has unique properties that help aerospace engineers optimize component performance.
Comparison with Other Coating Methods
HVOF coatings are often compared to other thermal spray methods like plasma spray and flame spray. Here is how HVOF stands out:
- Higher Density: HVOF coatings have fewer pores, reducing the risk of corrosion and wear.
- Greater Adhesion: The high velocity during application ensures stronger bonding to the substrate.
- Lower Oxidation: The HVOF process minimizes oxidation of the coating material, preserving its properties.
While plasma spray can achieve higher temperatures, HVOF is preferred for applications requiring superior wear resistance and mechanical strength.
Maintenance and Inspection of HVOF Coatings
Regular maintenance and inspection are essential to ensure the long-term performance of HVOF-coated components. Aerospace technicians check for signs of wear, cracking, and delamination. Early detection of coating damage allows for timely repairs, preventing more extensive issues.
Common inspection methods include:
- Visual Inspection: Identifies surface defects like cracks and peeling.
- Ultrasonic Testing: Detects internal flaws and delamination.
- Adhesion Testing: Measures the coating’s bond strength.
Proper maintenance practices maximize the lifespan of coated components, improving overall aircraft reliability.
Future Trends in HVOF Coatings
Research and development continue to improve HVOF technology. Some emerging trends include:
- Advanced Materials: New materials with improved thermal and mechanical properties are being developed to enhance performance.
- Automation: Automated HVOF systems improve coating consistency and reduce human error.
- Environmental Sustainability: Efforts to reduce emissions and waste during the coating process are gaining traction.
These advancements will further strengthen the role of HVOF coatings in aerospace, helping manufacturers meet evolving demands.
Conclusion
HVOF coatings provide essential protection for aerospace components, enhancing their durability, safety, and performance. By resisting wear, corrosion, and high temperatures, these coatings reduce maintenance costs and extend the lifespan of critical parts. As technology advances, HVOF coatings will continue to play a vital role in the aerospace industry.