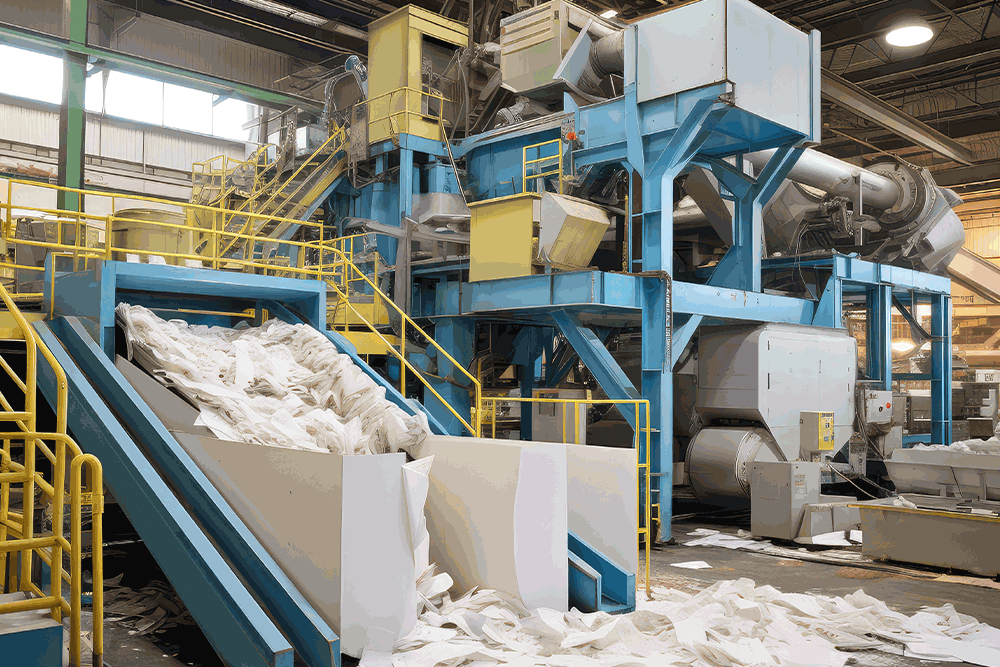
Choosing the Right Coating for Corrosion Protection in the Chemical Industry
Corrosion is a major challenge in the chemical industry, gradually damaging equipment and infrastructure. This problem affects efficiency, safety, and operational costs, making corrosion control a critical concern for businesses.
Without proper protection, machinery and storage units can deteriorate, leading to leaks, contamination, and potential hazards for workers. Additionally, repairs and replacements due to corrosion drive up maintenance costs and disrupt production schedules.
Globally, corrosion leads to billions in losses each year. Industries that rely on chemical processing must adopt effective preventive measures to protect valuable assets. Protective coatings are among the best solutions for combating corrosion, as they extend the lifespan of equipment and enhance performance.
Why Corrosion Protection is Essential in the Chemical Industry
Understanding Corrosion Types
Corrosion occurs in different forms, each presenting unique challenges depending on the environment and materials involved. Below are some of the most common types:
- Pitting Corrosion: Small, localized holes that penetrate metal surfaces, potentially leading to leaks and equipment failure.
- Galvanic Corrosion: Happens when different metals contact an electrolyte, causing one metal to corrode at a faster rate.
- High-Temperature Corrosion: Found in environments exposed to extreme heat and aggressive chemicals.
- Oxidation: A slow process where metal reacts with oxygen, forming rust and weakening structures.
Impact on Equipment and Safety
Corrosion affects:
- Structural Integrity: Weakens metal, leading to equipment failure.
- Safety: Increases risk of leaks, explosions, and chemical exposure.
- Maintenance Costs: Leads to frequent repairs and replacements.
- Operational Efficiency: Causes unplanned downtimes, disrupting production.
Types of Coatings for Corrosion Protection
Barrier Coatings
Barrier coatings create a protective layer over metal surfaces, preventing exposure to moisture, chemicals, and contaminants.
Examples: Emralon 310 and Molydag 250 by Acheson.
Sacrificial Coatings
These coatings corrode instead of the underlying metal, providing long-term corrosion resistance.
Examples: Molykote by Dow Corning and Chemlok 6254 by Lord Corporation.
Selecting the Right Coating for Specific Chemical Environments
Resistance to Specific Chemicals
Coatings must be selected based on chemical exposure:
- Acidic Environments: Require acid-resistant coatings.
- Alkaline Environments: Need coatings that withstand high pH levels.
- Saltwater Exposure: Demand coatings that prevent chloride-induced corrosion.
Example: Magni-approved coatings for extreme chemical exposure.
Temperature Resistance
High-temperature environments require specialized coatings.
Example: Xylan by Whitford, which resists heat and chemical exposure.
Benefits of Corrosion-Resistant Coatings in the Chemical Industry
- Extended Equipment Lifespan: Reduces wear and tear, increasing durability.
- Cost Savings: Lowers maintenance and replacement expenses.
- Operational Efficiency: Minimizes downtime and ensures smooth production.
Real-World Applications
Case Study 1: Protecting Equipment from Corrosive Chemicals
Metatech Thermal Spray Pvt. Ltd. applied Magni coatings to chemical processing equipment, significantly reducing wear.
Case Study 2: Extending the Life of Industrial Parts
Molykote 250 coatings helped a client double the lifespan of their mixers and reactors, reducing costs.
How Metatech Thermal Spray Pvt. Ltd. Can Help
Expert Solutions
With over 50 years of experience, Metatech provides high-performance corrosion-resistant coatings.
Trusted Brands
They offer solutions using brands like Acheson, Doerken, and Dow Corning.
Custom Coating Solutions
Metatech specializes in customized coatings tailored to specific environments.
Conclusion
Selecting the right coating is essential for preventing corrosion. By considering chemical exposure, temperature resistance, and operational requirements, businesses can improve:
- Equipment durability
- Safety standards
- Overall efficiency
Want to protect your equipment?
Contact Metatech Thermal Spray Pvt. Ltd. for expert consultation and customized solutions.
For more information on coatings, follow Bhavik Patel on LinkedIn.