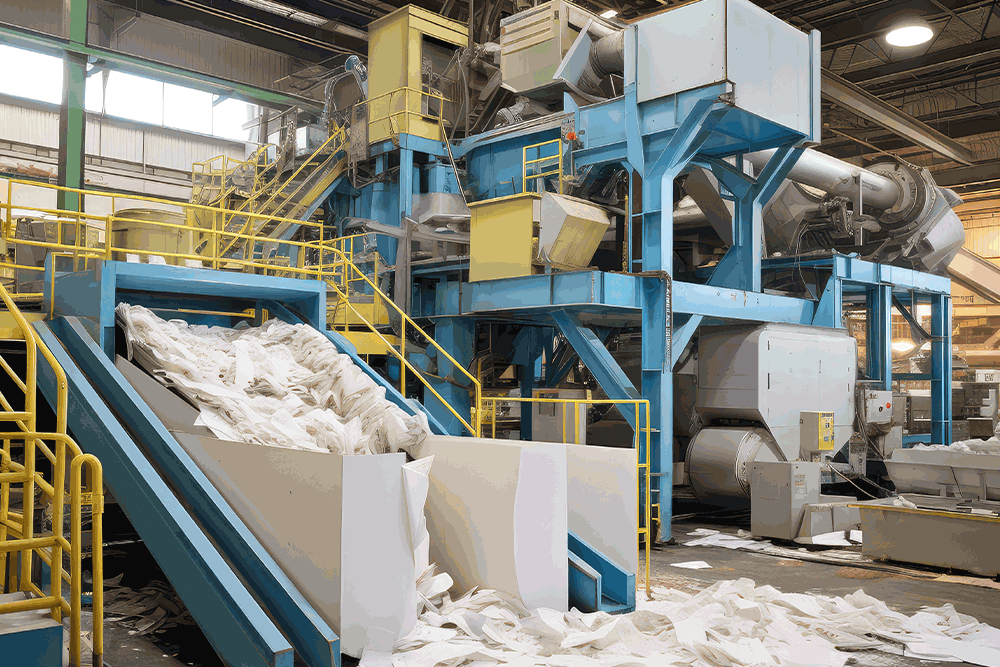
How Thermal Spray Coating Enhances Durability Efficiency
What is Thermal Spray Coating?
Thermal spray coating is a process where heated particles of metal, ceramic, or other materials are sprayed onto a surface to form a strong, protective layer. This coating acts as a shield against:
- Wear
- Corrosion
- High temperatures
- Other damaging factors
From jet engines to chemical plants and steel structures, thermal spray has become the go-to solution for protecting critical assets.
Enhancing Durability: Protecting Against Wear & Tear
1. Shielding Against Corrosion
Corrosion is a major issue for metal components, leading to structural weakening and costly repairs. Thermal spray coatings like zinc or aluminum create a protective barrier, preventing corrosive agents such as moisture, salt, and chemicals from damaging the metal.
Industries benefiting from corrosion protection: Oil & Gas, Chemical Processing, Marine Applications.
2. Fighting Wear & Abrasion
Machinery components face constant wear due to friction, dust, and rough surfaces. Thermal spray coatings, such as tungsten carbide or chromium carbide, offer superior hardness and wear resistance.
Example: Coated pump parts or turbine blades last significantly longer than uncoated ones.
3. Handling Extreme Temperatures
High-heat environments, such as gas turbines and engines, can cause premature component degradation. Thermal spray coatings, particularly ceramic-based materials, provide exceptional thermal resistance, ensuring that components remain functional under extreme conditions.
Efficiency = Better Performance, Less Downtime
1. Reducing Friction for Smooth Operation
Thermal spray coatings can be engineered to reduce friction between moving parts. This leads to:
- Smoother machinery operation
- Lower energy consumption
- Less heat generation
Example: Coated pistons and cylinders in automotive engines improve fuel efficiency and performance.
2. Improving Reliability & Uptime
Unplanned downtime due to equipment failure impacts productivity and profits. With a protective coating, components become more reliable, reducing the frequency of repairs and replacements.
3. Cost Savings Through Longevity
Although thermal spray coating requires an initial investment, the long-term cost savings are substantial. The benefits include:
- Extended component life
- Reduced maintenance costs
- Minimized downtime
- Higher return on investment (ROI)
Metatech: Delivering High-Quality Thermal Spray Coating Solutions
As a leader in the thermal spray coatings market, Metatech offers customized solutions for industrial challenges. Whether it’s:
- Corrosion protection
- Thermal resistance
- Wear prevention
Metatech ensures that your components perform efficiently.
Why Choose Metatech?
- Advanced Coating Techniques: Metatech offers solutions such as Thermal Spray Aluminium (TSA), Tungsten Carbide Coatings, and Ceramic Coatings.
- Cost-Effective Solutions: Metatech helps industries lower maintenance costs, reduce downtime, and extend the life of equipment.
Conclusion: Investing in Long-Term Durability & Efficiency
Thermal spray coating is no longer an option; it's a necessity for industries that rely on heavy machinery and high-performance systems.
If your business faces:
- Frequent component failures
- Rising maintenance costs
- Inefficient equipment performance
Thermal spray coatings could be the solution you need.
In an era where downtime can make or break success, investing in durability and efficiency isn’t just smart—it’s essential.
Get in Touch
Contact us today at www.thermalsprayworld.com to learn more about our coatings and how they can benefit your business.
For more updates and industry insights, follow our founder, Bhavik Patel, on LinkedIn.