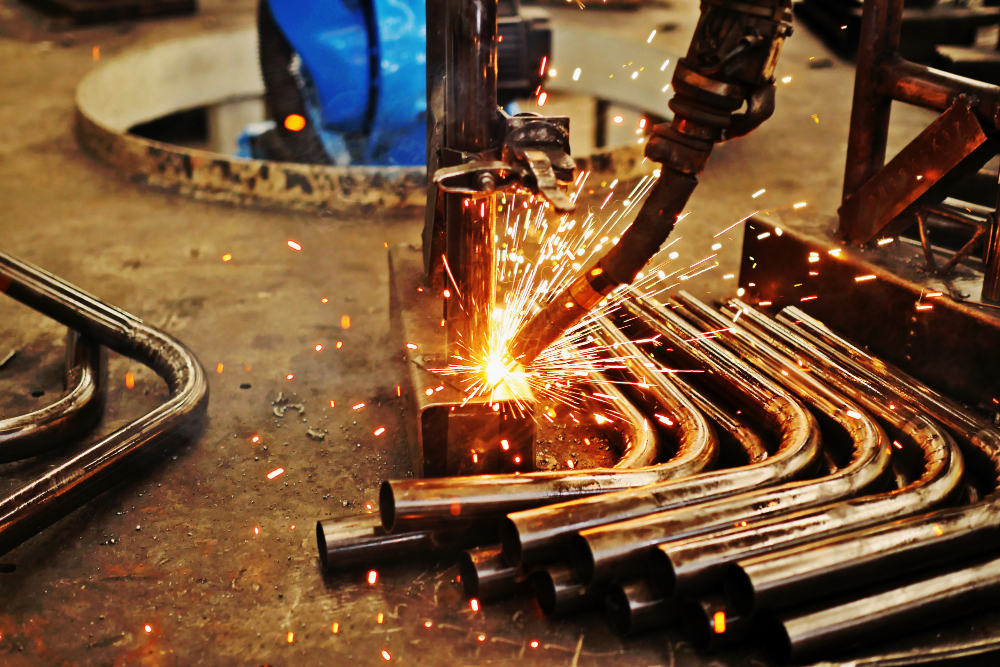
Introduction
Traditional coatings offer temporary relief from wear and corrosion.
So, our question is: Why choose a traditional coating when you can have an advanced one?
Metatech’s advanced coatings provide:
- Long-term performance
- Reduce maintenance needs
- Increase your equipment’s lifespan
At Metatech, we help steel mill operators maximise efficiency, reduce downtime, and extend the life of their equipment. Our expertise in manufacturing, refurbishing, and advanced coating technology is customised to meet the demands of Cold Rolling Mills (CRM), Continuous Galvanising Lines (CGL), and Hot Strip Mills (HSM).
In this article, we’ll walk you through how Metatech’s specialised solutions and facilities can improve your operations.
Key Applications for Mill Operations
Steel mills require specialised rolls to operate efficiently. Our coatings and refurbishment services are designed to make sure that each component performs reliably, even under high stress and extreme conditions. Here’s a look at some of the key rolls we service:
- Sink Pot Roll: For stable and efficient immersion processes in galvanising lines.
- Bridle Roll & Skin Pass Roll: Important for tension control and finishing processes in rolling mills.
- Internal and External Cooler Roll: Maintains optimal cooling during processing.
- Stabiliser, Deflector, and Path Line Rolls: Ensures alignment and stability throughout the line.
- ROT Roll, APC-TDR Roll, and Accumulator Roll: Provides control for roll positioning.
- Hearth/Furnace Roll & Switch Roll: Handles extreme temperatures in heating and cooling zones.
- Tension Leveller Roll and Chute Roll: Manages metal tension and material transfer.
We help your steel mill reduce wear and tear, lower maintenance costs, and increase overall uptime by refurbishing and coating these rolls.
Advanced Coating Solutions: The Metatech Advantage
Our coating solutions are designed to extend the life and performance of mill components, saving time and money in the long run. Here’s how our specialised coating methods work:
1. Boiler Tube Coating
- Twin Wire Arc Spray
- Porosity: Less than 5-6%
- Adhesion: Up to 5,000 psi
- Hardness: 55-60 HRC
- Coating thickness: Up to 500 µm
- Quick application for minimal downtime
- HVOF Spray
- Low porosity (less than 1%)
- Superior adhesion (up to 10,000 psi)
- Hardness: 65-70 HRC
- Uniform, smooth surface free of cracks
2. Converter Hood Coating
Protects against intense corrosion, abrasion, and thermal shocks common in steel melting environments. Our Inconel 625 coating over tubes increases service life, cuts shutdown costs, and minimises production loss due to wear and tear.
3. Thermal Spray Aluminium Coating on Caster Structures
Ideal for providing corrosion resistance in high-temperature environments. Unlike traditional paint, our aluminium coating handles high heat without peeling, ensuring long-lasting protection for caster structures.
Our Workshop Facility
Metatech’s expansive and fully equipped facilities help us to provide the best services for steel mill components. Our workshop covers an area of 25,000 square feet, housing the latest in coating and testing technology, including:
- Manufacturing and Heat Treatment Furnace: For custom roll production and durability enhancements.
- Cylindrical Grinding and Polishing: For smoothness of all coated surfaces.
- Non-Destructive Testing (NDT) Facility: For comprehensive quality assurance.
- Robotic Coating Facility: Equipped with a 6-axis robot, dust collector, acoustic chamber, and job rotator to deliver consistent coatings on components.
Our workshop is also fitted with two EOT cranes, each with a 15-ton capacity, making sure we can handle even the heaviest steel mill components with ease.
Partner with Metatech for Solutions
Do you want to upgrade your Sink Pot Rolls?
Do you want to protect Converter Hoods?
Or do you want to improve the performance of caster structures?
Metatech has the expertise and facilities to meet your needs. Let’s discuss how our advanced coatings and refurbishment services can optimise your steel mill operations, save costs, and keep your production running efficiently.
Contact us today at www.thermalsprayworld.com to learn more.
For more details around the coatings, you can also follow our founder, Bhavik Patel, on LinkedIn.